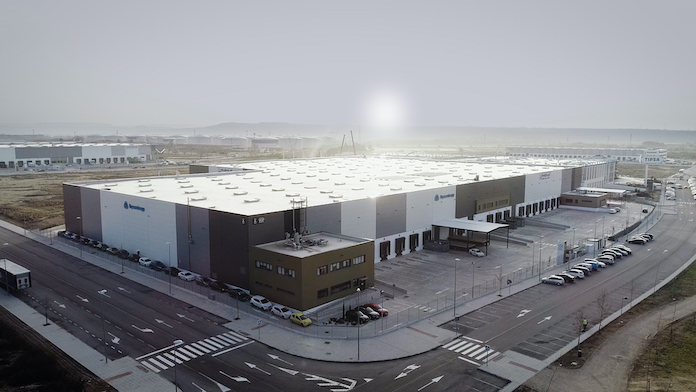
En San Fernando de Henares (Madrid) se encuentra el primer almacén de piezas de repuesto inteligente para el mantenimiento y la reparación de ascensores, a nivel mundial, de ThyssenKrupp. Más de 6.000 metros cuadrados que revelan la innovación que se realiza en la filial española de la compañía. Y no es casualidad: España cuenta con el mercado más importante de ascensores de la empresa de elevadores; es aquí donde, de forma natural, la matriz fija sus principales objetivos. Así, el proyecto, que nace como piloto en España –el primero de diez centros repartidos por el mundo–, tiene la intención es llegar a convertirse en la base central de la compañía en todo el sur europeo.
La inauguración, realizada esta misma semana, se ha realizado por todo lo alto. El propio CEO, Peter Walker, ha estado presente en el evento. Y él mismo se ha encargado de recordar por qué es importante este centro de almacenamiento inteligente. El objetivo del almacén tecnológico es el de “mantener una disponibilidad total de todos los repuestos para nuestros operarios, optimizando su logística a través de servicios de smart data, análisis y procesamiento de los datos recogidos en tiempo real. El análisis de datos inteligentes realiza los mismos procesos logísticos ahorrando un 30 % del tiempo en comparación con los almacenes tradicionales”.
Darío Vicario, CEO de ThyssenKrupp Elevator en España, Portugal y África, ha declarado en la presentación que, en el sector de la movilidad, el servicio es lo más importante. “Para minimizar los tiempos de inactividad se necesita una solución inteligente y actualizada. Eso es lo que proporciona el nuevo almacén de Madrid. Representa la máxima eficiencia, y pronto servirá a más países fuera de España”.

Pero, ¿cómo funcionará? Con una inversión de 3,5 millones de euros, unos 9.800 códigos de piezas y componentes diferentes para las reparaciones y las actuaciones predictivas y capaz de atender más de 1.400.000 pedidos anuales –lo cual implica un aumento del 400 % en comparación con el anterior almacén–, el centro propone, simplemente, reducir el tiempo de inactividad de los ascensores. Tarea sencilla a priori, pero no tan fácil en la práctica.
En un tour guiado por las instalaciones, ThyssenKrupp ha explicado cómo funciona el almacén, y también, cómo sigue funcionando aun con las piezas de repuesto fuera del espacio. “Queremos garantizar la disponibilidad de piezas de repuesto las 24 horas del día y distribuirlas de forma inmediata a los técnicos. Con ello, reducimos el tiempo de espera entre la solicitud de las piezas por parte de los técnicos hasta su entrega e instalación. Todo ello supone un 10 % de ahorro al año en desplazamientos de los técnicos para buscar material en la delegación. Además, se mejora en un 20 % la espera del usuario en resolución de averías, ya que los técnicos dispondrán del componente a su alcance en todo momento”.
MAX: todo comienza con una (posible) avería
Para arreglar ascensores primero debe haber una avería. O no, ya que gracias a la tecnología actual se puede predecir la vida útil de los dispositivos. Para ello, ThyssenKrupp cuenta con una herramienta llamada MAX, “el primer sistema predictivo del mercado” –instalado ya en más de 120.000 ascensores–, que, gracias a su algoritmo basado en el Internet de las Cosas, “realiza un seguimiento exhaustivo del estado de los componentes del ascensor para localizar las posibles incidencias, como el desgaste de las piezas y su esperanza de vida”, ha explicado Walker.
Al estar conectado con la nube de Microsoft, es capaz de enviar un aviso al técnico con el problema que ha detectado en el dispositivo, “e incluso cuáles son las piezas de recambio y las herramientas necesarias para solucionar la avería. Transforma toda esa recogida de datos en smart data, aplicando el procedimiento adecuado en cada momento en función de unas necesidades concretas, una vez os datos estén debidamente tratados”.
Así, en principio, no se necesita una avería para comenzar a trabajar. Una vez detectado el problema (o el posible problema), el técnico identifica con su propio móvil qué pieza de repuesto necesita. De hecho, la nueva instalación de San Fernando de Henares “permite una organización única y perfectamente catalogada de los componentes a disposición de los técnicos en todo momento. Todas las piezas figuran en un sistema limpio y ordenado que permite a los operarios acceder a distancia para todo lo que precisen para las reparaciones, reduciendo así los trayectos innecesarios de un lugar a otro y sin intermediarios”, asegura.

Del mismo modo, los técnicos pueden acceder a la base de datos y solicitar, también desde sus móviles, todo cuanto necesitan, sin tener que acudir a recoger el pedido: la entrega se hará directamente desde el Almacén de San Fernando de Henares al punto de recogida convenido. “El objetivo es mantener a los técnicos equipados siempre con piezas de repuesto, evitándole así a los clientes las largas esperas entre los procesos de diagnóstico y el arreglo”. “Es el final de la cadena del smart service. Queremos que haya un 100 % de disponibilidad, que los clientes no tengan que esperar”, ha apuntado también Carlos Pajares, director de Producto y Sostenibilidad de ThyssenKrupp.
La sostenibilidad que traerá San Fernando de Henares
Como no han dejado de remarcar en el evento de inauguración del almacén inteligente de ThyssenKrupp, la sostenibilidad ha sido un pilar importante para su creación. “Se prevé que el consumo energético del transporte se duplique para 2050 frente a los niveles del año 2000, situando el sector en una posición de debilidad frente a la volatilidad de precios y la escasez de los combustibles fósiles. Según el IPCC, en torno al 5,5% de las emisiones globales de gases de efecto invernadero se deben a la actividad logística”.
Así, “al suprimir un número innecesario de trayectos para trasladar los componentes de las reparaciones a los almacenes de las sucursales y los destinos», se reducirá notablemente el impacto de las emisiones producidas por los vehículos en el medio ambiente. “Nuestro compromiso ecologista va todavía más allá, con la sustitución de todo el embalaje del que dispone en Iberia por soportes reciclables para el empaquetamiento de las piezas: todas las existencias de paquetes serán completamente ecológicas, reutilizables y respetuosas con el medio ambiente. Podemos hablar de que la tecnología nos da las posibilidades para promover la interoperabilidad y la eficiencia en las operaciones que llevan a un futuro completamente sostenible a medio plazo”, aseguran.
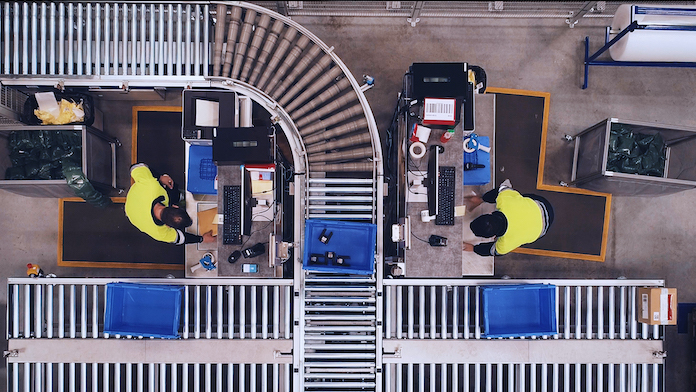
Artículo publicado en innovaspain.com